Concreto para obras offshore: Desafios de logística
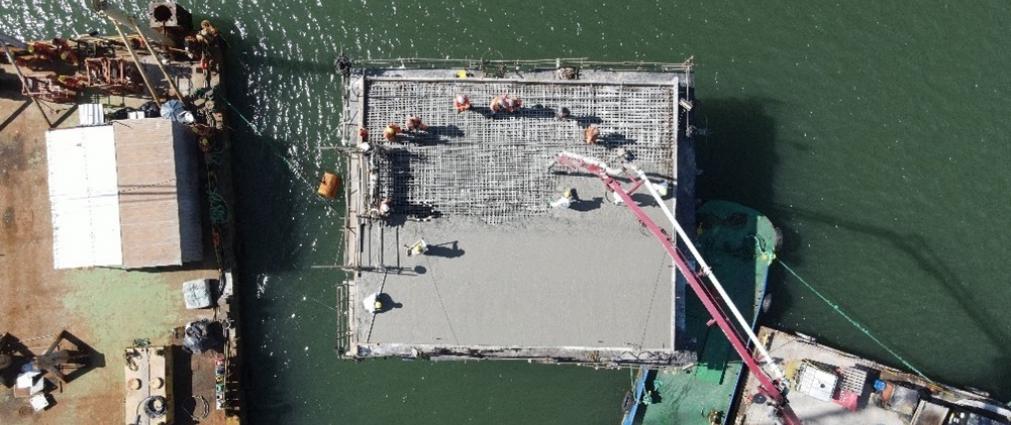
Em 2021, a OEC iniciou a implantação de uma planta de recebimento e estocagem de gás natural liquefeito (GNL) e regaseificação de gás natural (fase gasosa). Situado na Baía de Babitonga, no Município de São Francisco do Sul em Santa Catarina. Este projeto visa proporcionar uma oferta adicional de gás para a Região Sul do Brasil.
O escopo contempla a construção da infraestrutura portuária de um terminal marítimo em concreto armado, a 300 m da faixa de areia da Praia do Capri, em São Francisco do Sul – SC. Este terminal (obra civil) é composto de dois dolphins de atracação, quatro dolphins de amarração e uma plataforma operacional.
Foram previstas no projeto 14 estacas inclinadas para cada dolphin de atracação, 12 estacas inclinadas para cada dolphin de amarração e nove estacas verticais para a plataforma operacional. As estacas são revestidas por camisas metálicas de 1016 mm de diâmetro e concretadas, total ou parcialmente, após a escavação e/ou cravação. As superestruturas, executadas sobre as estacas, são constituídas por blocos de concreto armado com 1,50 metros de altura, executados em três etapas de concretagem, em camadas de 50 cm de espessura.
As operações de concretagens foram executadas com a utilização de betoneiras embarcadas em balsa flutuante. A distância do ponto de embarque, localizado no Ferry Boat em laranjeiras, até o ponto de aplicação era de 16 km, o equivalente a nove milhas náuticas.
Devido à grande distância entre o ponto de embarque das betoneiras e o local da concretagem, tornou-se necessário desenvolver um estudo para a adequação do traço do concreto, de forma a preservar suas características / trabalhabilidade até o momento da aplicação. Isto foi possível por meio do uso de aditivos específicos para retardar o tempo de início de pega.
Considerando-se potenciais interferências e imprevistos durante o processo de execução, optou-se pelo desenvolvimento de um traço com início de pega de no mínimo 10 horas, como contingência. Nesta análise, levou-se em consideração o grande transtorno da eventual necessidade de descarte do concreto, devido ao risco do material “endurecer” nos balões das betoneiras, em razão do tempo elevado de navegação no retorno.
O desafio imposto pela logística motivou a mobilização de consultoria técnica especializada, para ajudar no desenvolvimento do traço e ensaios de laboratório necessários. Após a análise da viabilidade, foram executadas dosagens experimentais na própria usina de concreto para atestar, através de ensaios, a efetividade do traço.
A fase de execução das atividades de concretagem comprovou que o uso de tecnologia no desenvolvimento de um traço mais adequado ao processo foi uma decisão acertada, pois viabilizou a execução de diversos eventos de concretagem em uma única viagem.
PRINCIPAIS CONTRIBUIÇÕES
Em um primeiro momento, é necessário compreender o cenário em se encontrava a implantação do terminal marítimo. O ponto mais próximo identificado para embarque das betoneiras de concreto foi o da rampa de acesso do Ferry Boat que faz a travessia São Francisco do Sul – Itapoá, o qual se encontrava a 16 km do local de implantação do terminal (Figura 1). O tempo de navegação para o deslocamento da balsa carregada com oito betoneiras, a depender das condições da maré, variava entre um mínimo de 2h:30min e máximo de 3h:30min.
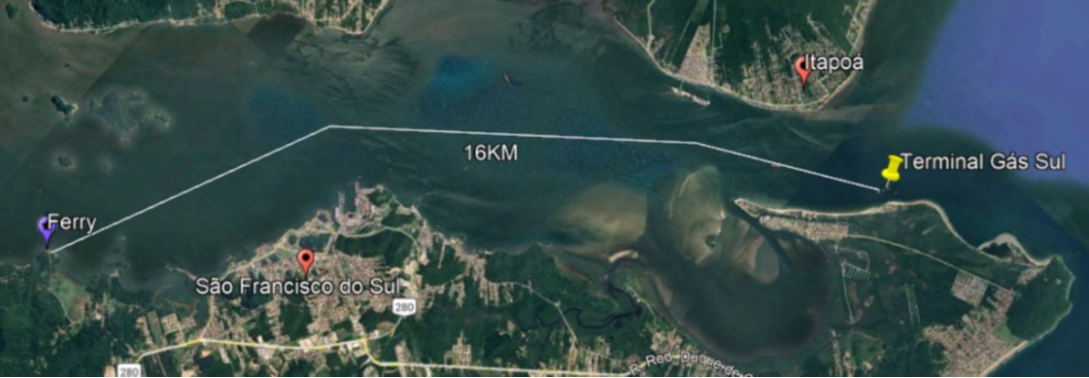
Figura 1. Trajeto e distância entre o cais e o ponto de concretagem.
Outro ponto importante a ser considerado: a navegação de retorno da balsa de concreto iniciava somente após o lançamento da última betoneira embarcada. Trata-se de um fator fundamental a se considerar na decisão dos planos de concretagem pois, ao contrário de uma obra convencional em terra, as betoneiras retornavam à usina todas ao mesmo tempo. Portanto, a decisão de um novo ciclo dependeria da celeridade do processo na viagem antecessora. Diante disto, em uma concretagem que necessitasse de oito betoneiras (ou 64 m3), a primeira a ser carregada seria embarcada junto à oitava.
Com o andamento dos trabalhos, iniciou-se a execução dos blocos das superestruturas e, para estes, o projeto previa três etapas de concretagem (com 64 m3 cada). A primeira etapa necessitaria ser totalmente preenchida para resistir aos esforços das demais. O determinante para a decisão da subdivisão em 3 etapas foi a capacidade de transporte de concreto por viagem, limitado a 64 m3.
Em um carregamento de 64 m3, por exemplo (cada betoneira com 6 m3), havia a necessidade de se considerar:
1. O tempo de carregamento por betoneira, de aprox. 30min; ou 4h de carregamento para as oito betoneiras;
2. O tempo de deslocamento da usina de concreto até o ponto de embarque do Ferry, com duração de cerca de 40min;
3. O tempo necessário para embarque das betoneiras no Ferry Boat;
4. O tempo de navegação;
5. O tempo de manobra para atracação a contrabordo das balsas nos pontos de lançamento.
Tendo-se em conta os tempos envolvidos (conforme computado acima) e a possibilidade de ocorrência de interferências e imprevistos, a equipe técnica envolvida buscou soluções que permitissem obter um traço adequado, com o tempo de pega prolongado. Adicionalmente, implementou-se melhorias nas condições de navegação, além da substituição de alguns equipamentos por outros mais adequados ao processo.
Com relação ao problema de adequação do traço ao tempo de pega, a equipe técnica envolvida, com apoio da consultoria externa mobilizada, logrou em desenvolver um traço com um tempo de início de pega de 15 h; superior, portanto, ao que havia sido especificado inicialmente como necessário. Este estudo foi desenvolvido em função do tipo de cimento, aditivos e das características dos agregados próximas a região de São Francisco do Sul.
Outro ponto de melhoria identificado no decorrer do processo foi a substituição do rebocador até então utilizado para fazer a navegação por outro de maior potência. Esta substituição permitiu reduzir em 1 h o tempo de navegação marítima, o que viabilizou a realização de até dois ciclos de concretagem no mesmo dia.
Ainda referente ao tempo de navegação: com o apoio de um engenheiro naval, observou-se que a redução do lastro da balsa utilizada no transporte das betoneiras não afetava a sua estabilidade. Estando mais leve, a balsa ainda pôde navegar com segurança e com uma velocidade maior.
Finalmente, verificou-se ser possível reduzir o consumo do aditivo VMA de 0,3% para 0,1%, algo que trouxe uma grande economia no custo do concreto.
Diante das inovações implementadas, foi possível reduzir o tempo de navegação, otimizar o consumo de diesel dos rebocadores e betoneiras e aumentar a produtividade da mão de obra responsável pelo fornecimento de concreto.
METODOLOGIA CONSTRUTIVA
Logística envolvida na operação de concretagem
A operação logística para viabilizar a concretagem pode ser resumida nas seguintes etapas:
1. Carregamento das betoneiras às 04h:00 da madrugada na central de concreto, localizada no centro da cidade de São Francisco do Sul - Este horário era ajustado em função dos horários das marés de enchente e vazante (Figura 2);
2. As betoneiras se direcionavam para o local de embarque, no cais de atracação da balsa. Este local era utilizado como rampa de acesso de embarque para a travessia de São Francisco do Sul para Itapoá;
3. Embarque de maneira organizada das betoneiras na balsa, para que a operação de concretagem pudesse ser realizada na mesma ordem do carregamento na central. É importante ressaltar que o posicionamento dos caminhões na balsa era definido com base no estudo de estabilidade, elaborado pelo engenheiro naval (Figura 3);
4. Após o embarque, a balsa era conduzida por rebocadores por até 3h30min de navegação até o local da concretagem;
5. Ao chegar no ponto de aplicação, a balsa é atracada: (i) Em uma outra balsa com um sistema de fundeio por meio de cabos de seda ou; (ii) Nas estacas em blocos já executados ou; (iii) Permanecia estabilizada por meio dos rebocadores;
6. Após o lançamento do concreto e descarga de todas as betoneiras, a balsa então retornava para o ponto de desembarque e os caminhões retornavam para a central de concreto. Durante a viagem de retorno, a equipe de lançamento realizava a limpeza preliminar nos balões com água. O expurgo era então descartado em caçambas de entulho, que estavam alocadas na balsa
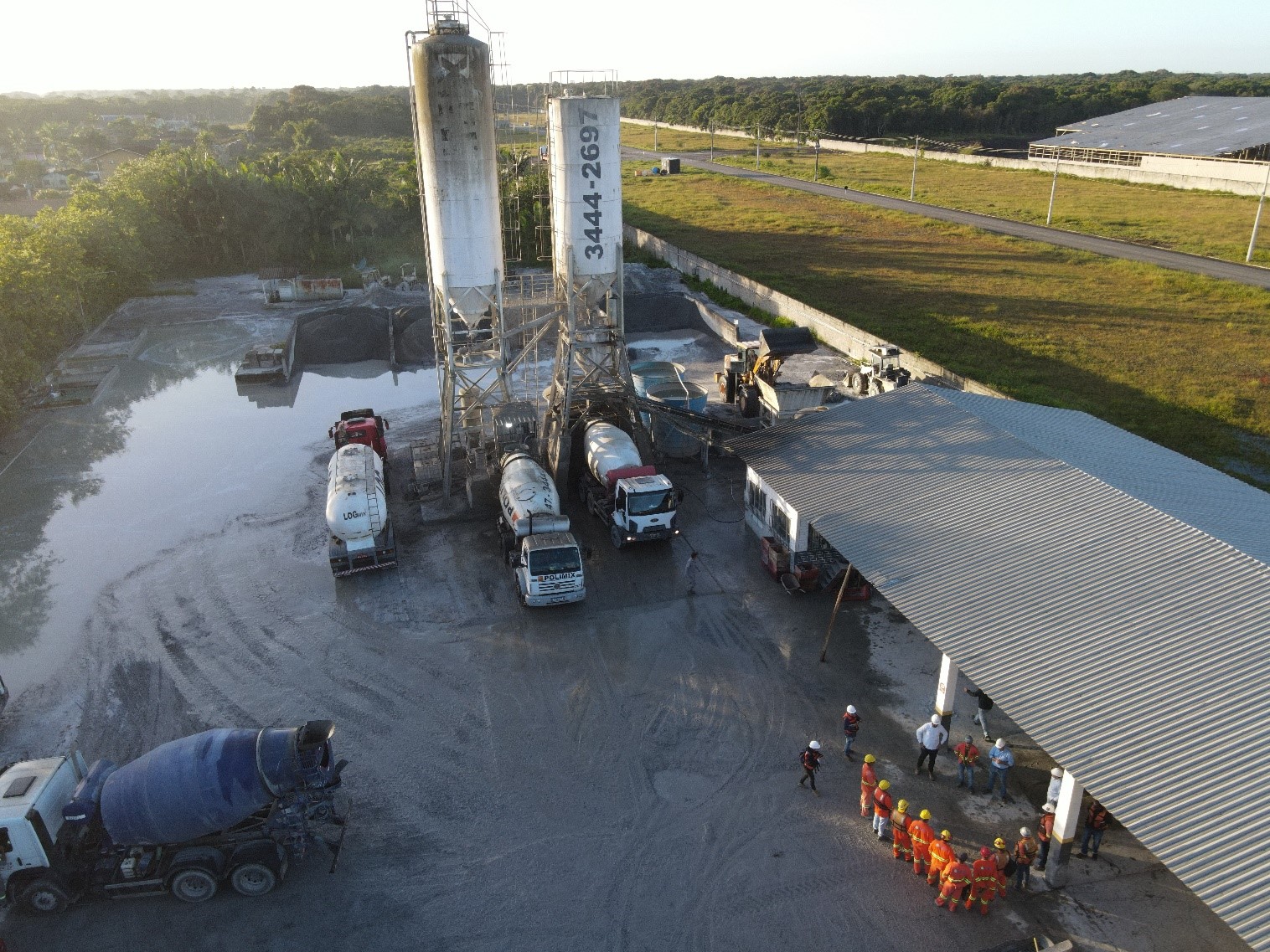
Figura 2. Carregamento das betoneiras na central de concreto (Polimix).
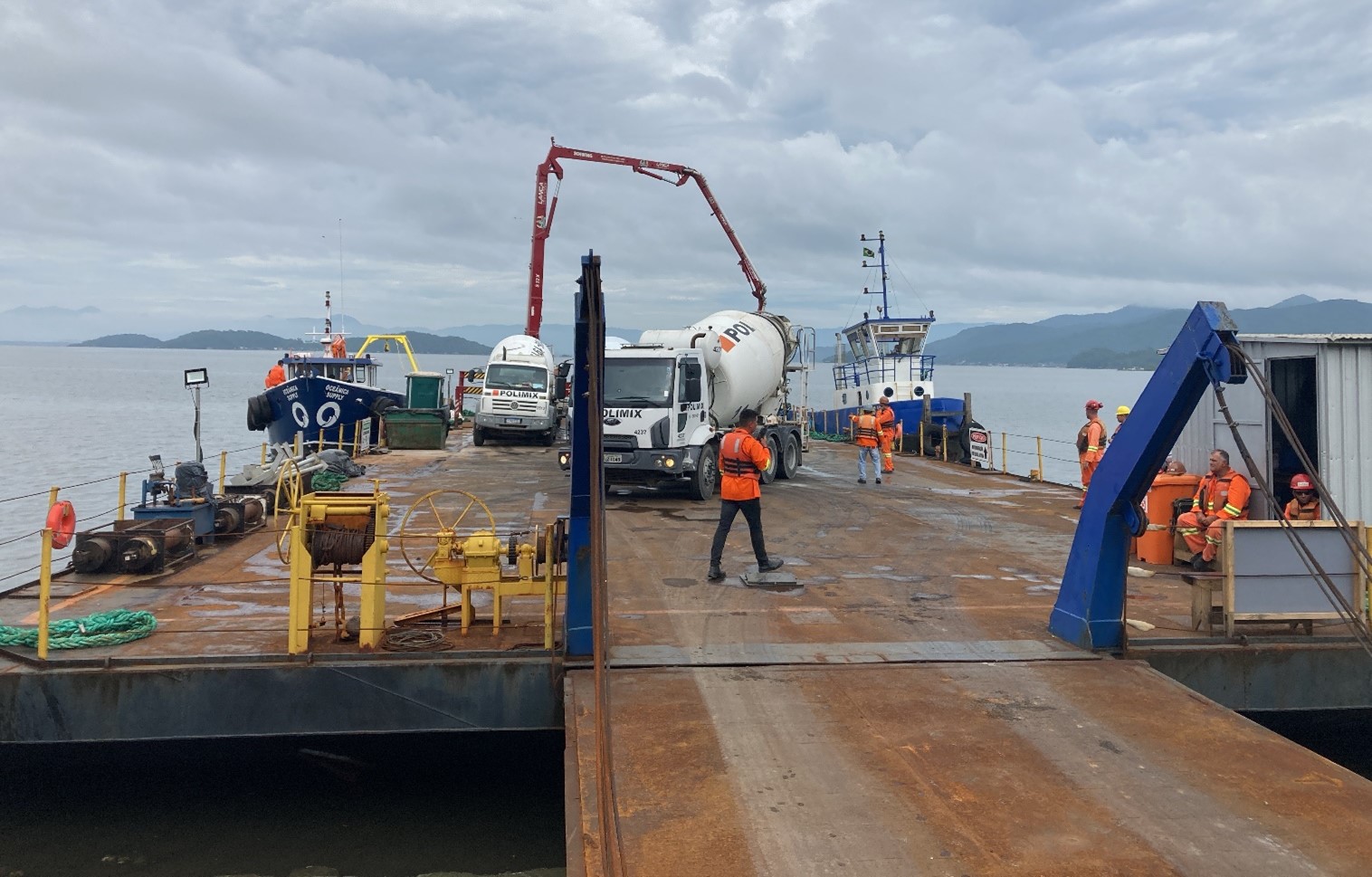
Figura 3. Embarque sequencial das betoneiras nas balsas.
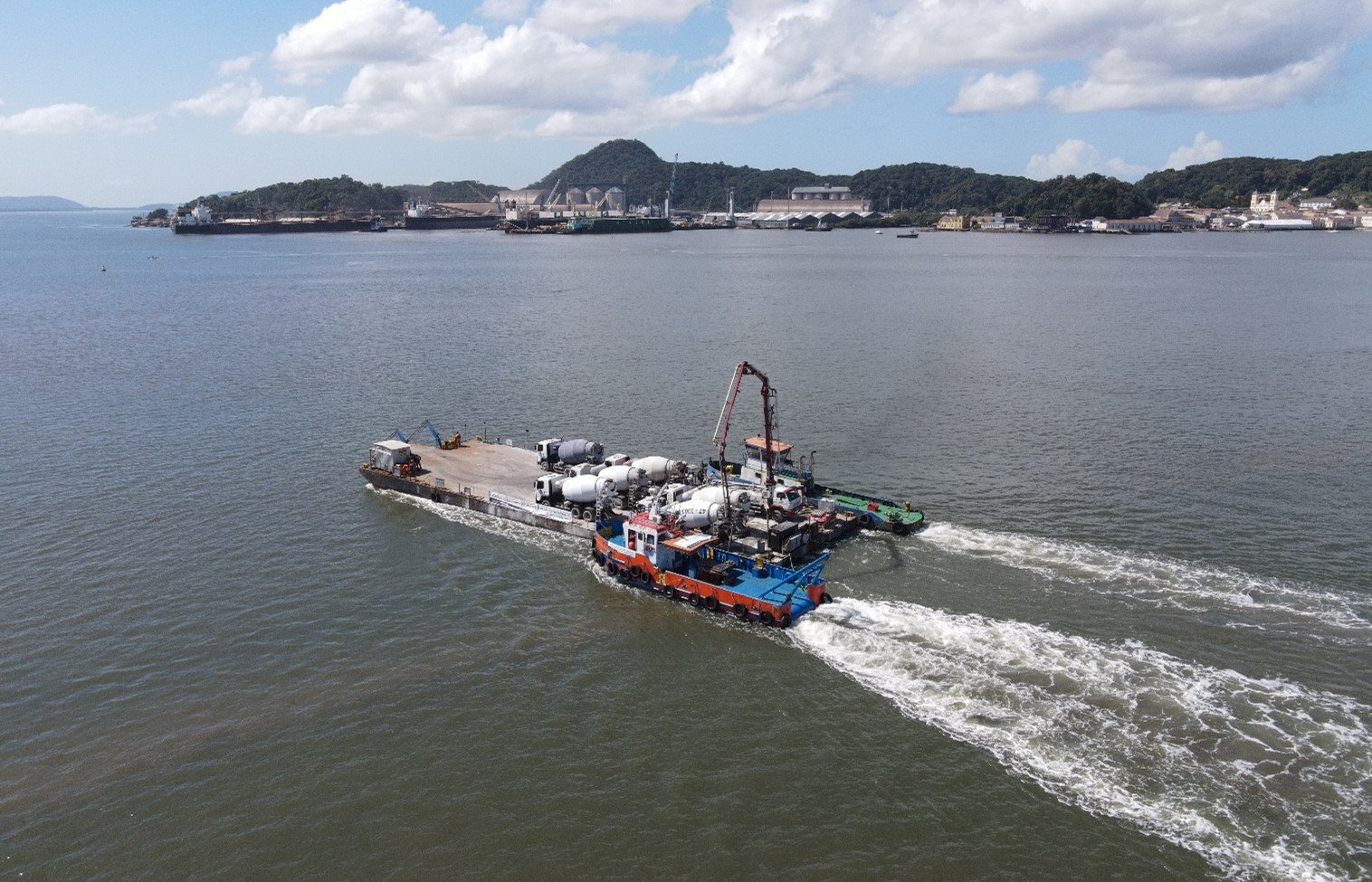
Figura 4. Condução da balsa por rebocadores até o local da concretagem.
PROBLEMAS OBSERVADOS
O problema de maior impacto identificado foi a formação de “torrões” de concretagem após um certo período de mistura nas betoneiras. A formação destes “torrões” poderia danificar a estrutura dos balões das betoneiras no momento da rotação. Além disso, a qualidade do concreto poderia resultar comprometida, com prejuízos à trabalhabilidade durante o lançamento do material com as bombas-lança.
Outro ponto observado foi o acúmulo de concreto no interior do balão após a concretagem, observado durante a operação de lavagem, a qual era dificultada principalmente pelas condições locais e pelo uso do aditivo modificador de viscosidade.
Esses problemas foram resolvidos com a adição de super-plastificantes no momento do lançamento, provendo-se também uma melhor orientação técnica para as equipes encarregadas do lançamento do concreto.
RESULTADOS OBTIDOS
As inovações implementadas aqui resumidas permitiram um menor tempo de navegação e a otimização das operações de concretagem. Com estas melhorias no processo, conseguiu-se reduzir o tempo ocioso das equipes e o consumo de Diesel em horas improdutivas dos rebocadores e betoneiras. Isto possibilitou uma redução importante dos custos de operação, em torno de 8% do custo total previsto.
É importante ressaltar que os ganhos auferidos com esta inovação transcendem o aspecto econômico. Destaca-se que houve uma menor emissão de metais pesados na atmosfera, devido à redução da queima do diesel de rebocadores e caminhões-betoneira.
Finalmente, com a redução do tempo de navegação, aumentou-se o número de viagens por dia, resultando em um maior número de eventos de concretagens, com reflexos importantes na produtividade global.
___________________________________________________________________
OEC – Odebrecht Engenharia e Construção
Obra do TGS – Terminal Gás Sul
Autores:
Alvaro Maia
Clauss Ocké
Daniel Wanderley
Henrique Doca
Iuri Ferreira
Orres Vicente
Gerente de Contrato
Ricardo Corregio
Elaboração de texto / Contatos OEC:
Sarah Barbosa Martins Silva
Daniel Lepikson